Basic Info.
Model NO.
DMH Series High Temperature Purifying Sterilizer
Customized
Customized
Condition
New
Warranty
1 Year
After-sales Service
1 Year
Operating Chamber: 600X500X750
Operating Chamber: 600X500X750
Outside Dimension: 1650X900X1750
Outside Dimension: 1650X900X1750
Cleanness Grade: 100 Grade
Cleanness Grade: 100 Grade
Circulating Blowing Rater(M3/H): 2540
Circulating Blowing Rater(M3/H): 2540
Supplementary Blowing Rate (M3/H): 300
Supplementary Blowing Rate (M3/H): 300
Transport Package
Plywooden Case
Specification
CE
Trademark
SPM
Origin
China
HS Code
84192000
Production Capacity
1000 Set Per Year
Product Description
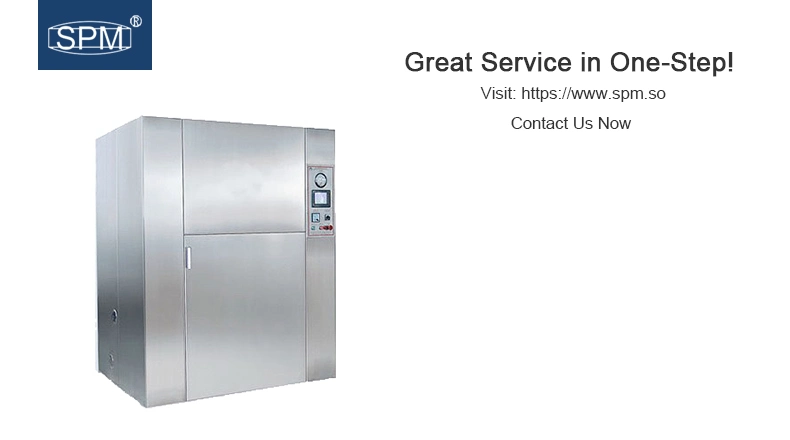
DMH Series High temperature purifying sterilizing oven
Usage and Brief Introduction:
1.DMH series high temperature purifying sterilizing ovens are applicable to the bacteria-killing, pyrogen-removing and drying sterilization of solid objects such as Schering bottles, ampoule bottles, aluminum caps and metal or glass vessels.
2.DMH series purifying split-door ovens are the products of a new generation which have been developed in recent years by our company and have all passed certification in hundreds of pharmaceutical enterprises in China. The control system of the equipment is advanced and sensitive. A batch of key components such as PLC programmable controller, man-machine interface touch screen, micro-manometer, automatic moisture-expelling valves, inflammable gas concentration tester and so on are all made in Japan, USA or Chinese Taiwan, thus providing a guarantee to the quality of the products. The perfect 100grade laminar flow purifying system conforms to the requirement of GMP norms.
3.DMH series products offer a choice of selection to the users. In terms of configuration and size, the product can be customized according to the usage, site, output and so on required by the users.
4.Operating principle: Place the baking pallets, bottles or trolley loaded with the materials or objects into the oven and start PLC programmable control system. The blower for internal circulation operates; and heating starts. At the same time, the butterfly valve opens; and the temperature inside the drying oven rises rapidly. Under the action of the blower for internal circulation, dry hot air enters into the oven body through the high-temperature-resisting and high-efficiency filters. Under the action of micro-porous regulation, a homogeneously-distributed air is formed for transmission into the oven body. The dry air absorbs the moisture remaining on the surfaces of bottles(materials or objects)for its entrance into the heating channel, resulting in evaporation and outward expulsion. The dry air flows in directional circulation under the action of the blower for expulsion of water vapor. With the gradual reduction of water vapor and the simultaneous intermittent supplementation of fresh filtered air, the inside of the oven body exhibits the state of micro positive pressure. With the termination of the constant temperature, the process control comes to an end. Delivery of air or forced cooling (with flow-in of water) starts; and the automatic butterfly valve enters the state of closure, giving an audio and visual alarm for opening the door and removing the bottles.
Main Technical Parameter:
Model | DMH-1 | DMH-2 | DMH-3 | DMH-4 |
Operating chamber dimensions(mm)(WxDxH) | 600×500×750 | 800×800×1000 | 1000×1000×1200 | 1000×1200×1500 |
Outside dimensions(mm)(WxDxH) | 1650×900×1750 | 1850×1200×1950 | 2050×1400×2150 | 2050×1600×2450 |
Heating power(KW) | 9 | 15 | 22 | 28 |
Circulating blower power(KW) | 1.1 | 2.2 | 3.0 | 4.0 |
Supplementary blower power(KW) | 0.06 | 0.18 | 0.18 | 0.25 |
Moisture-expelling blower power(KW) | 0.18 | 0.25 | 0.37-300 Room temperature | 0.75 |
Designed temperature scope ºC Room temperature | -300 Room temperature | -300 Room temperature | -300 Room temperature | -300 Room temperature |
Cleanness grade | 100grade | 100grade | 100grade | 100grade |
Circulating blower blowing rate(m3/h) | 2540 | 2700 | 2900 | 3200 |
Supplementary blowing rate(m3/h) | 300 | 408 | 408 | 408 |
Usage and Brief Introduction:
1. DMH series high temperature purifying sterilizing ovens are applicable to the bacteria-killing, pyrogen-removing and drying sterilization of solid objects such as Schering bottles, ampoule bottles, aluminum caps and metal or glass vessels.
2. DMH series purifying split-door ovens are the products of a new generation which have been developed in recent years by our company and have all passed certification in hundreds of pharmaceutical enterprises in China. The control system of the equipment is advanced and sensitive. A batch of key components such as PLC programmable controller, man-machine interface touch screen, micro-manometer, automatic moisture-expelling valves, inflammable gas concentration tester and so on are all made in Japan, USA or Chinese Taiwan, thus providing a guarantee to the quality of the products. The perfect 100grade laminar flow purifying system conforms to the requirement of GMP norms.
3. DMH series products offer a choice of selection to the users. In terms of configuration and size, the product can be customized according to the usage, site, output and so on required by the users.
4. Operating principle: Place the baking pallets, bottles or trolley loaded with the materials or objects into the oven and start PLC programmable control system. The blower for internal circulation operates; and heating starts. At the same time, the butterfly valve opens; and the temperature inside the drying oven rises rapidly. Under the action of the blower for internal circulation, dry hot air enters into the oven body through the high-temperature-resisting and high-efficiency filters. Under the action of micro-porous regulation, a homogeneously-distributed air is formed for transmission into the oven body. The dry air absorbs the moisture remaining on the surfaces of bottles(materials or objects)for its entrance into the heating channel, resulting in evaporation and outward expulsion. The dry air flows in directional circulation under the action of the blower for expulsion of water vapor. With the gradual reduction of water vapor and the simultaneous intermittent supplementation of fresh filtered air, the inside of the oven body exhibits the state of micro positive pressure. With the termination of the constant temperature, the process control comes to an end. Delivery of air or forced cooling (with flow-in of water) starts; and the automatic butterfly valve enters the state of closure, giving an audio and visual alarm for opening the door and removing the bottles.
2. DMH series purifying split-door ovens are the products of a new generation which have been developed in recent years by our company and have all passed certification in hundreds of pharmaceutical enterprises in China. The control system of the equipment is advanced and sensitive. A batch of key components such as PLC programmable controller, man-machine interface touch screen, micro-manometer, automatic moisture-expelling valves, inflammable gas concentration tester and so on are all made in Japan, USA or Chinese Taiwan, thus providing a guarantee to the quality of the products. The perfect 100grade laminar flow purifying system conforms to the requirement of GMP norms.
3. DMH series products offer a choice of selection to the users. In terms of configuration and size, the product can be customized according to the usage, site, output and so on required by the users.
4. Operating principle: Place the baking pallets, bottles or trolley loaded with the materials or objects into the oven and start PLC programmable control system. The blower for internal circulation operates; and heating starts. At the same time, the butterfly valve opens; and the temperature inside the drying oven rises rapidly. Under the action of the blower for internal circulation, dry hot air enters into the oven body through the high-temperature-resisting and high-efficiency filters. Under the action of micro-porous regulation, a homogeneously-distributed air is formed for transmission into the oven body. The dry air absorbs the moisture remaining on the surfaces of bottles(materials or objects)for its entrance into the heating channel, resulting in evaporation and outward expulsion. The dry air flows in directional circulation under the action of the blower for expulsion of water vapor. With the gradual reduction of water vapor and the simultaneous intermittent supplementation of fresh filtered air, the inside of the oven body exhibits the state of micro positive pressure. With the termination of the constant temperature, the process control comes to an end. Delivery of air or forced cooling (with flow-in of water) starts; and the automatic butterfly valve enters the state of closure, giving an audio and visual alarm for opening the door and removing the bottles.
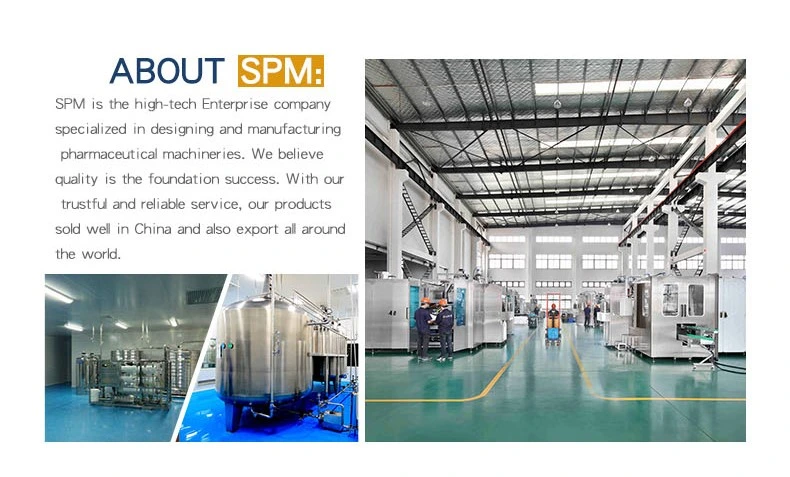
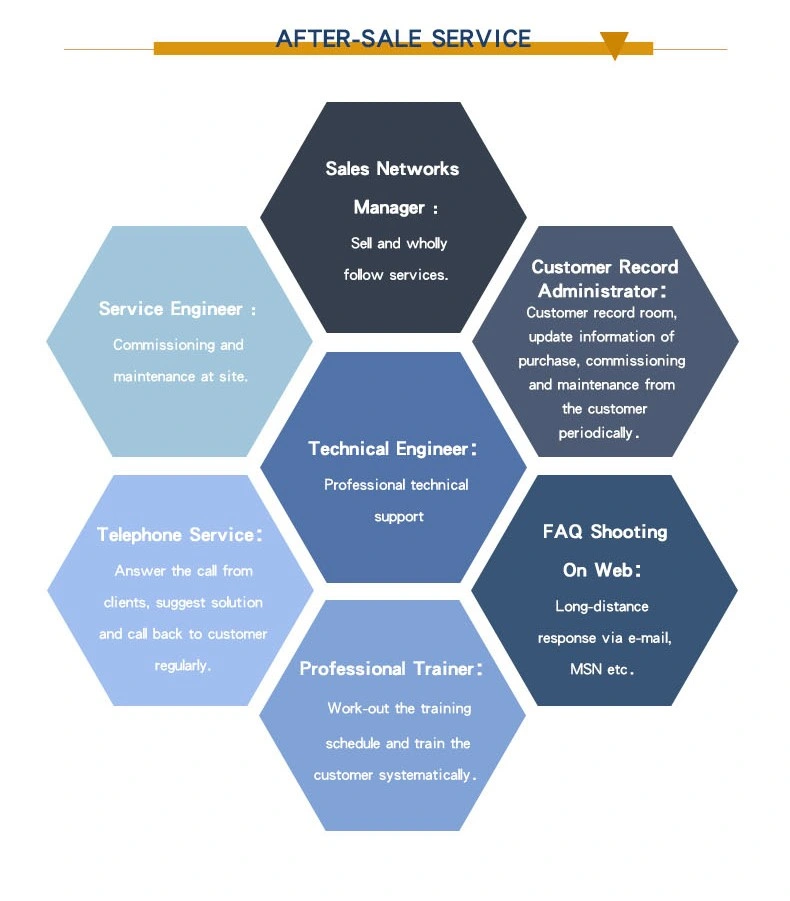
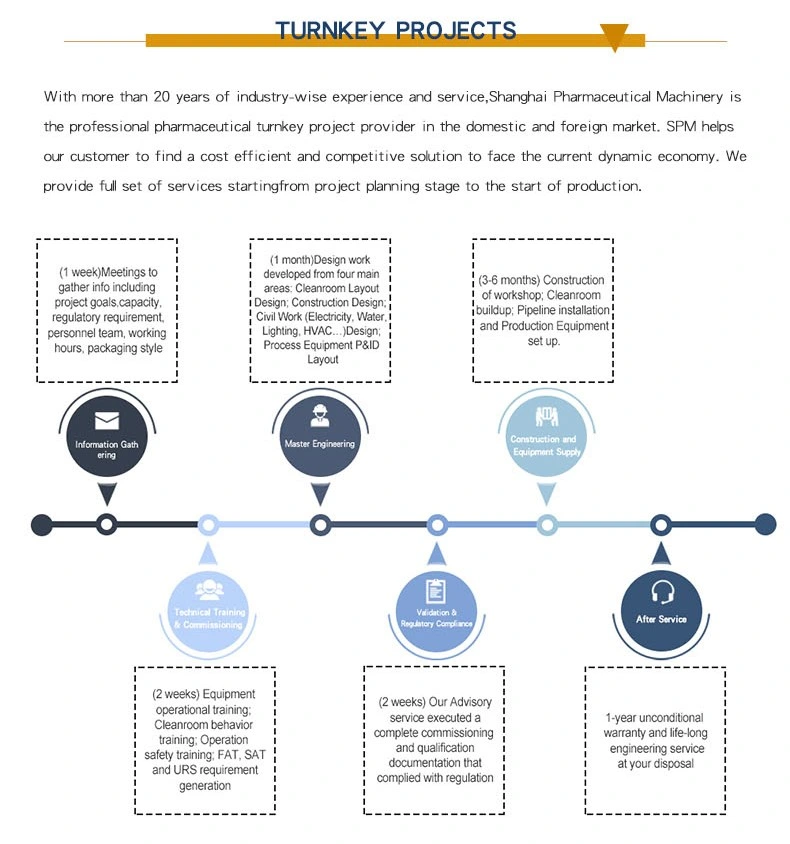
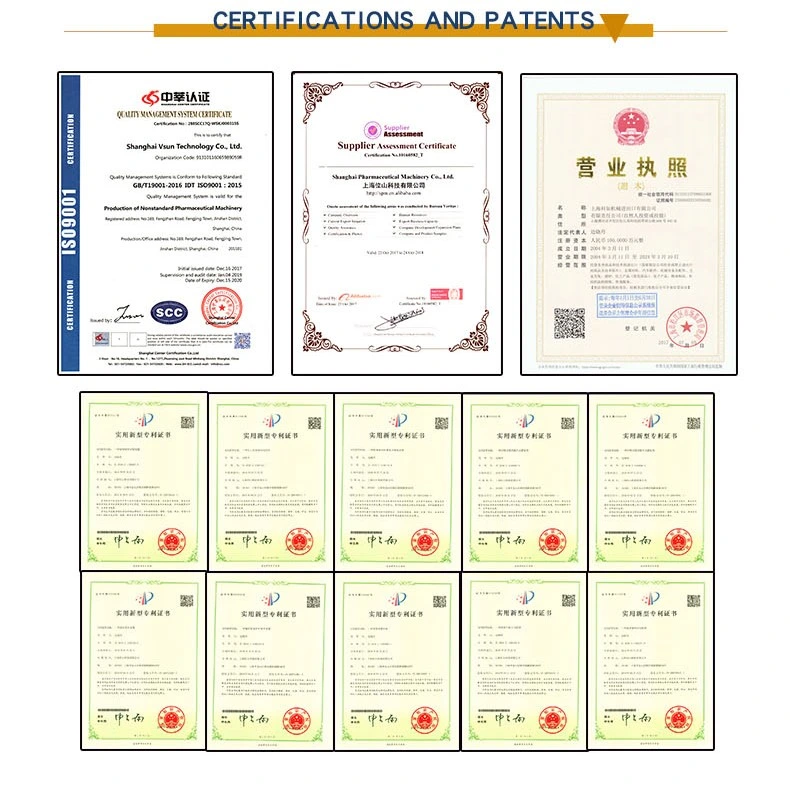
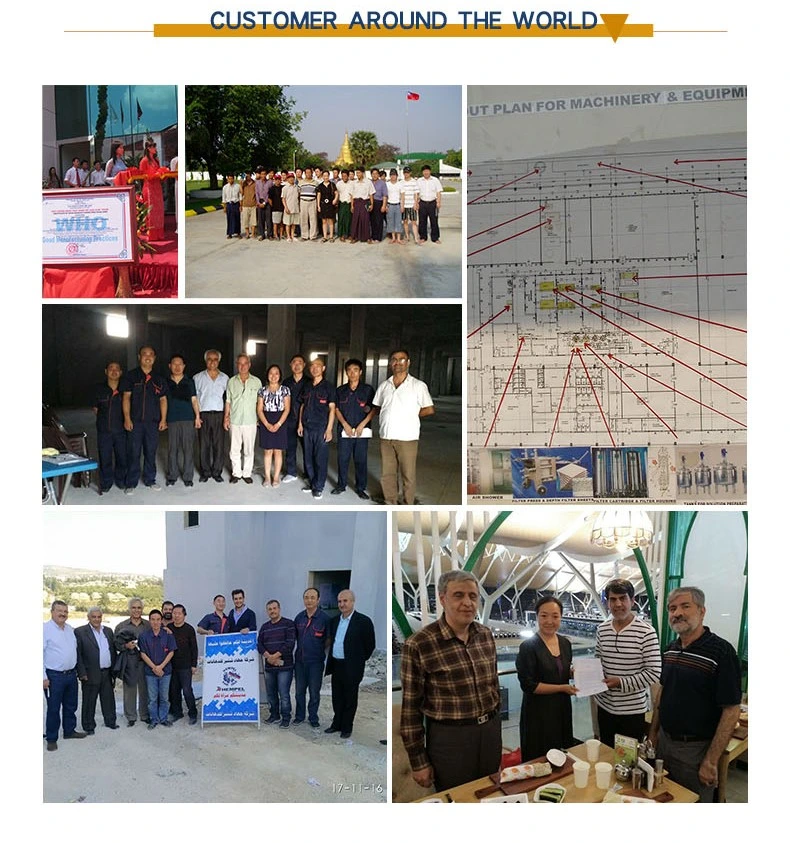
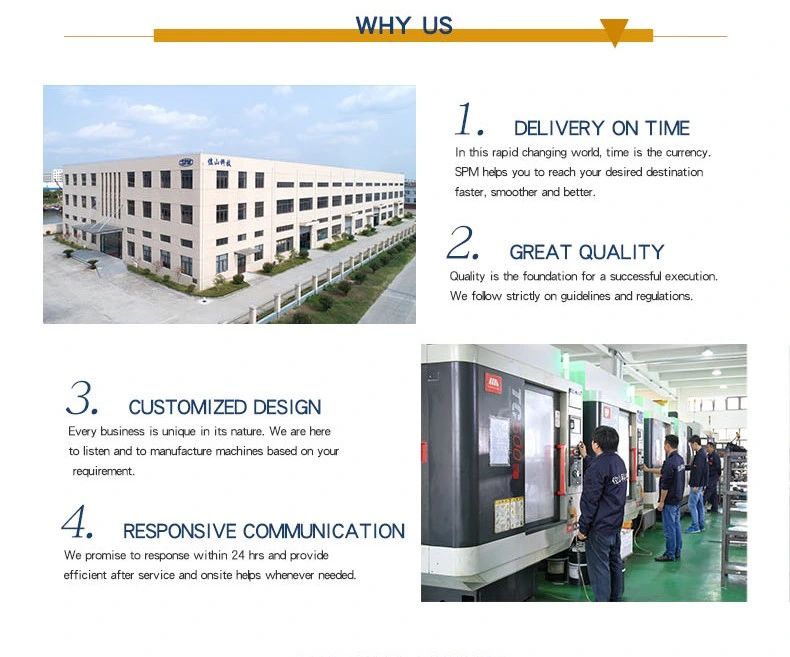
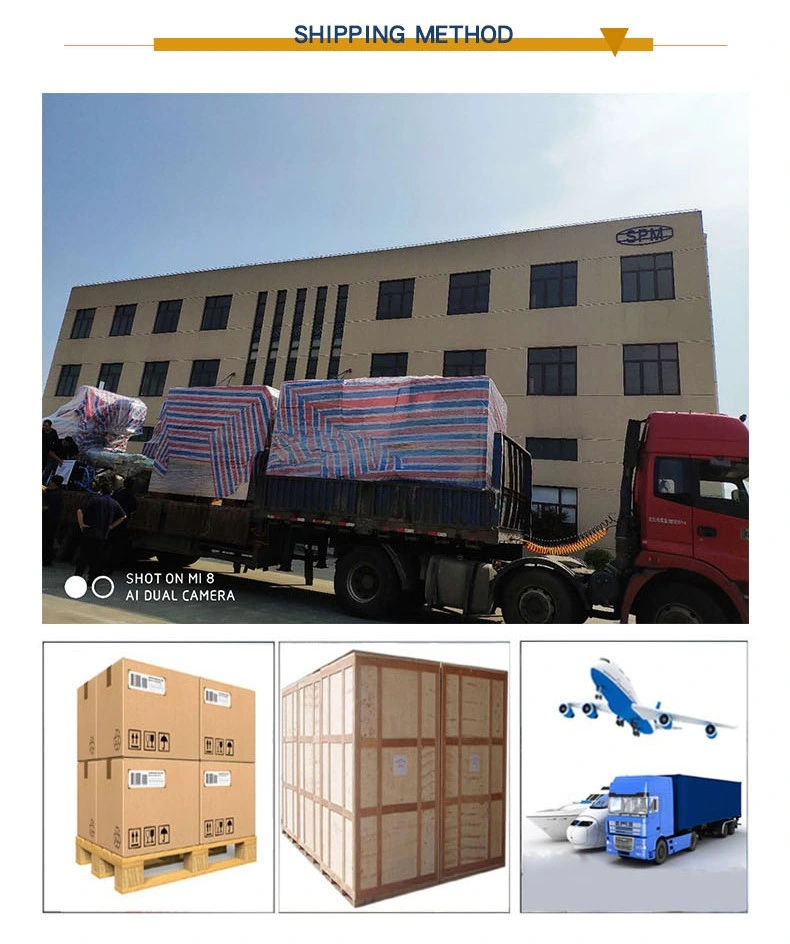
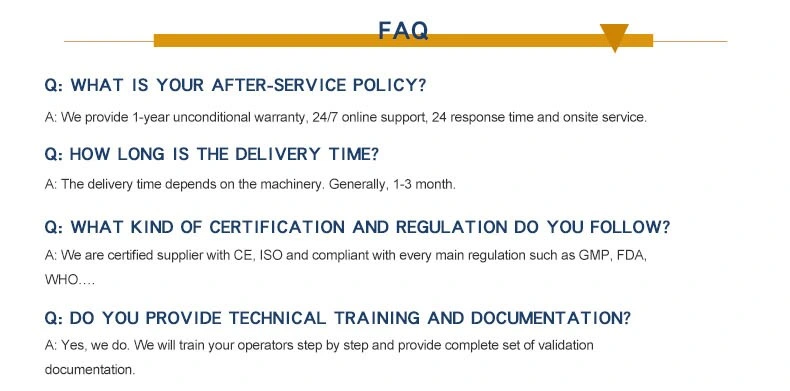