Basic Info.
Product Description
Mushroom Substrate Grow Bags Steam Sterilizer for Mushroom Cultivation
Description:
The usual procedures for mushroom culture include: preparation of the growth substrate, bagging (placing the growth substrate in an airtight bag or bottle), sterilization, inoculation, culture, fruiting formation, harvesting and drying.
Why do I need to sterilize mushroom medium?
Mushrooms can only grow in a specific growing medium. Mushroom mycelium should be the only rapidly growing organism in the growth matrix. Other microorganisms in the mushroom growth matrix may compete with the mushroom mycelia for growth space and inhibit or destroy the formation of a complete colony of mushroom mycelia. Therefore, in the industrial production of edible fungi, high temperature sterilization (that is, autoclave sterilization at 121 ° C) or pasteurization (60-100 ° C) is usually used to sterilize the growth substrate.
The general operation is: the growth substrate into a container (plastic bottle or bag), and then the container into the high temperature steam chamber sterilization, steam room temperature is usually about 100ºC, placed for about 8-20 hours (depending on the type of mushroom and sterilization conditions), to ensure that the growth substrate pure and free from microbial invasion.
Using our mushroom substrate sterilizer, various mushroom-like growth substrates are sterilized by high temperature saturated steam (around 100 ° C) with pressure. steam sterilization creates the ideal environment for mycelium colonization to produce fruit and growth.
Features:
1. The outer cavity and inner cavity are made of high-grade stainless steel 304, 316 and 316L, with acid resistance and corrosion resistance.
2. PLC automatic control, touch screen operation interface. Dynamic display of sterilization process and temperature, pressure, time parameters, parameters can be modified according to the actual situation.
3. Equipped with a number of safety features, including door interlocking system, overpressure protection, low water level protection, overload and short circuit.
4. Use vacuum pump to deal with cold air, vacuum in the chamber, and dry through the sandwich, so that the material in the chamber can be dried quickly. Liquid loop reduces cycle time and improves performance.
5. Doors are designed to provide adequate user and device security. In the two-door unit, the clean room and the aseptic room can be separated to avoid cross-contamination.
6. Products that can be sterilized: Metallic instruments; Rubber items (not thermal-sensitive); Textiles;
7. Available programs. It has 5 standard validated programs and2 test programs (Bowie & Dick, Leakage test). Up to 100 new (and fully configurable) terilization cycle can be created.
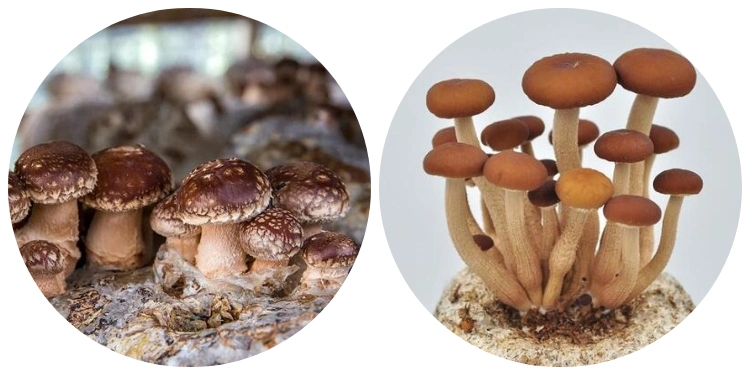
Specification:
Design pressure | 0.245Mpa | Vacunm | -0.095Mpa |
Working Pressure | 0.22Mpa | Steam Source Pressure | 0.4-0.6Mpa |
Design Temperature | 139ºC | Water Source Pressure | 0.1-0.3Mpa |
Working Temperature | 134ºC | Compressed Air Pressure | 0.5-0.7Mpa |
Specifications | Overall Dimensions | Chamber Size | Steam Consumption | Power | Water Consmption | Net Weight |
Model | L*M*H(mm) | L*W*H(mm) | (kg/cycle) | (KW) | (kg/cycle) | (kg) |
Single/Double Door | ||||||
YG-0.1 | 825*1080*1600 | 630*400*480 | 15 | 1 | 80 | 380 |
YG-0.25 | 895*1220*1720 | 760*600*600 | 20 | 1.5 | 150 | 650 |
YG-0.36 | 1195*1220*1720 | 1000*600*600 | 25 | 1.5 | 150 | 760 |
YG-0.6 | 1245*1300*1880 | 1050*680*850 | 30 | 2 | 200 | 1100 |
YG-0.8 | 1595*1300*1880 | 1400*680*850 | 35 | 3 | 250 | 1300 |
YG-1.2 | 1695*1370*1960 | 1500*750*1100 | 40 | 3 | 300 | 1900 |
YG-2.5 | 3195*1370*1960 | 3000*750*1100 | 75 | 4.5 | 450 | 2800 |
YG-5.0 | 3635*1800*2200 | 3400*1000*1500 | 150 | 7.5 | 600 | 4500 |
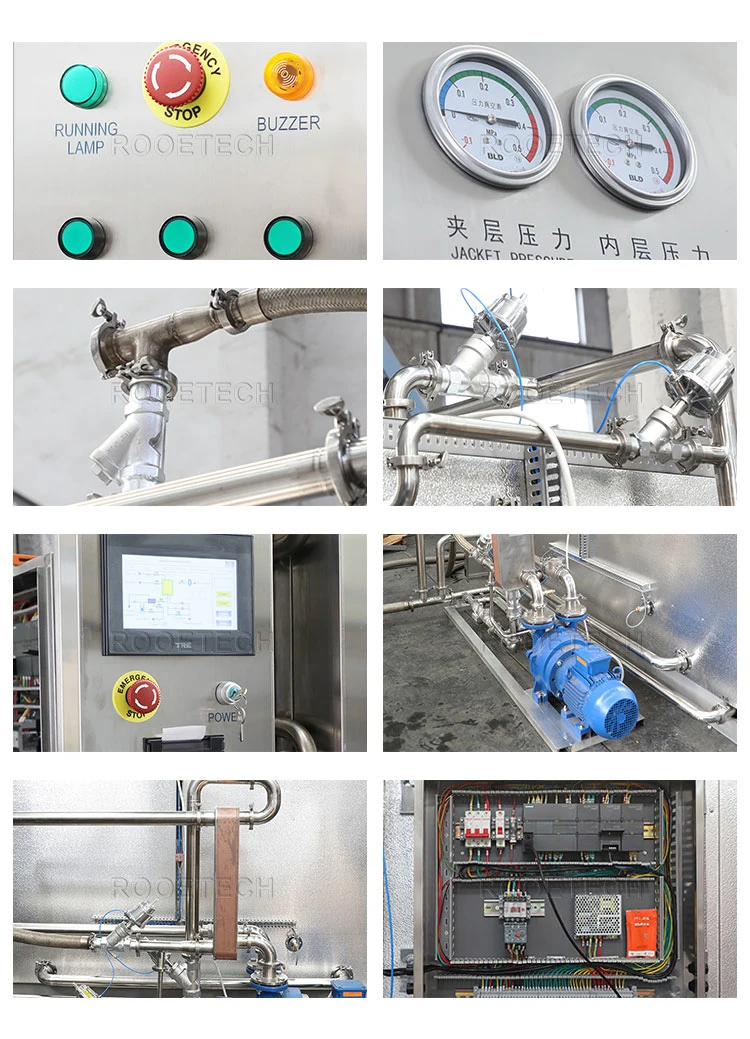
Optional monitoring system:
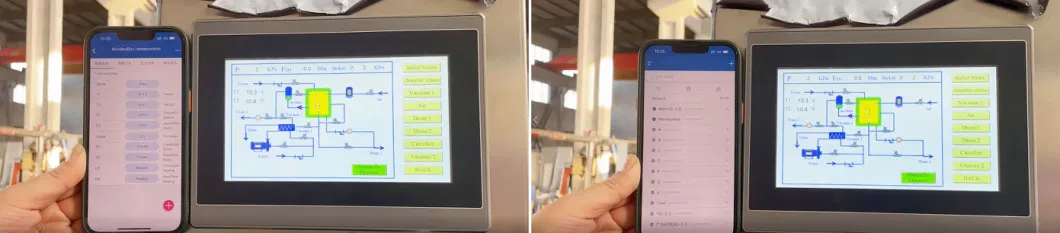
Company Information:
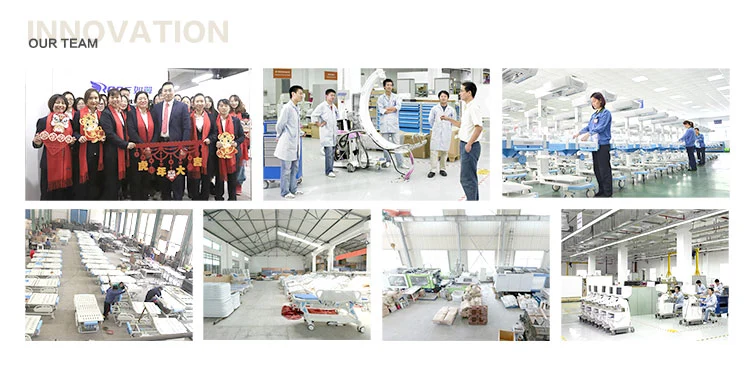
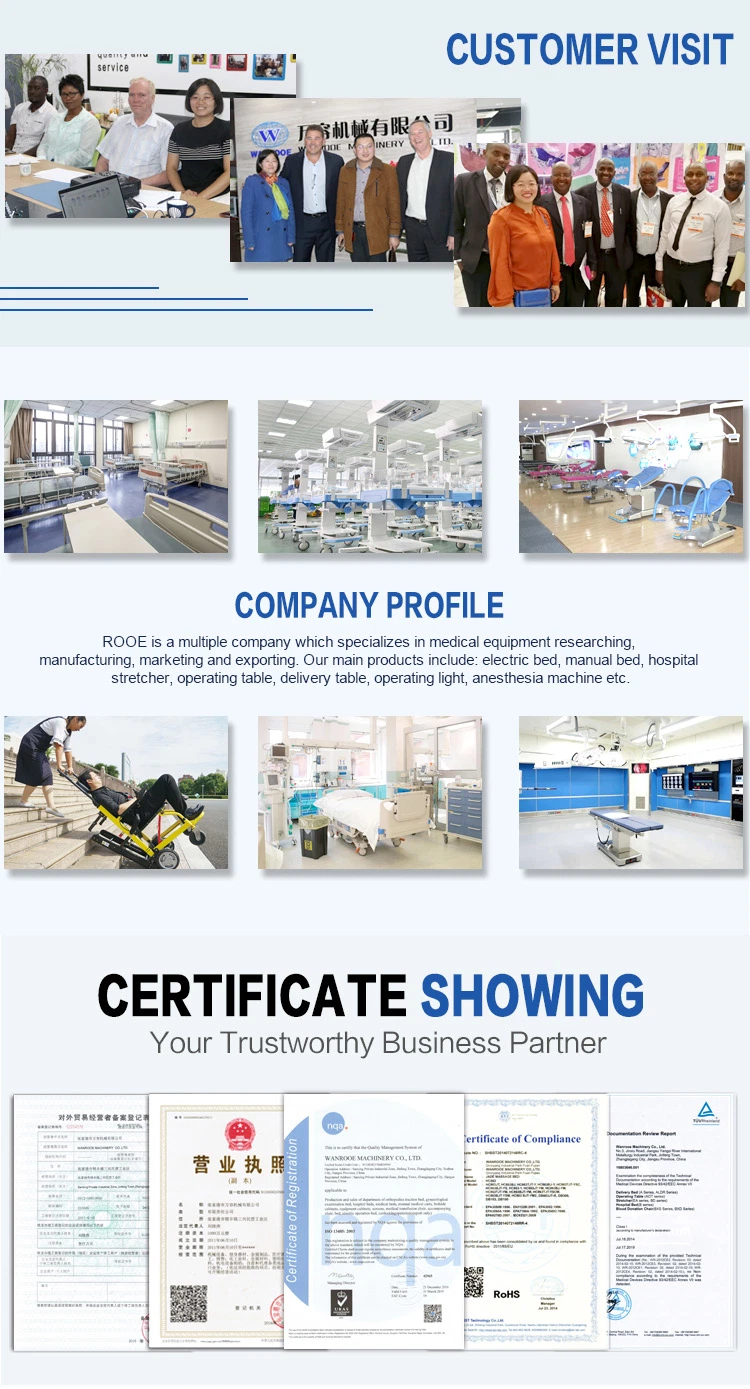