Basic Info.
Product Description
YG Hospital Equipment Medical Class B Dental Pulsation Vacuum Steam Autoclave Sterilizer for for Biomedicine1.General
Pulsating vacuum sterilizer is strictly designed and manufactured in accord with GMP technical Standard. It has passed ISO9001 quality management qualification standard and ISO13485:2003 Certificate of Quality Management System for Medical Devices.
It adopts PLC and man-computer interface automatic program control. The relevant data and curve can be saved and printed automatically.
This autoclave is suitable for pharmaceutical factory, hospital, scientific research institute and other units to sterilize and dry asepsis clothes, rubber goods, metal instruments, culture medium, etc.
2.Structure characteristic and working principle
(1) The sterilizer chamber is constructed from SUS316.Internal surfaces are highly polished to facilitate cleaning. A stainless steel mesh strainer protects the drain port from blockage by debris.
(2) The insulation material is made of aluminium silicate and covered with completely SUS304.
(3) The autoclave adopts double doors. Product will be loaded through loading door located in class D area and unloaded through unloading door in class B area.
They are automatic lock reconciliation lock by cylinder via push buttons on the control panel.
The operator can pull the door open or close manually.
Mechanical, electrical and software interlock devices prevent improper operation. The door is automatically sealed at the start of the cycle. Limit switches sense the door position to prevent the start of the cycle or utilities from entering the chamber until the door is fully closed and locked.
The door seal is a silicon rubber 'O' ring. On commencement of a process, the gasket is pressed against the rear face to the door by compressed air.
(4) Pipeline system is consisted of air filter,vacuum pump,steam trap,pressure controller,etc.
A highly efficient liquid ring pump is provided to effectively remove air from within the chamber. The vacuum pump is connected in series with an efficient condenser(a heating exchanger) to assist air removal and protect the vacuum pump from excessive.
(5)Automatic control system adopts PLC and HMI.
The color touch screen can to show the running process, sterilization parameters like temperature, pressure, sterilization time, etc.
In addition, The sterilization data and curve will be printed out by the Micro printer or transfer
into USB disk.
(6)Safety valves: Safety valves are provided on the chamber and jacket.
(7)Pressure gauges: Pressure gauges mounted in fascia are provided for:
Chamber pressure
Jacket Pressure
(8)The system shall have an E-Stop mechanism designed to stop all physical movement of the
equipment immediately.
3.Working procedure of sterilization
The autoclave controlled with optional operation or manual operation.
It will be used for sterilization of the following:
- Vacuum test program
- Instruments
- Rubber Plugs
- Aluminium Cap
- Rubber gloves
- Clean room dress
- Liquid disinfectants
Process flow
The autoclave control with optional automatic operation or manual operation.
We will preset many programs for customers.
All these programs are editable by users.
- Dynamic pre-vacuum:
Pulling vacuum in the chamber, and then while still pumping out air, allowing steam into the
chamber. This way, the air is removed from the chamber with no heat build-up on the material. - Pressure pulsing:
The aim is to provide rapid removal of non-condensable gases and condensates and to pre-heat the
material prior to sterilization. - Sterilization:
Steam injection into the chamber until sterilization temperature is achieved. When the working
pressure and temperature are obtained in the chamber, sterilization time begins. If the temperature
falls below the minimum sterilizing temperature. - Drying:
Pulling vacuum in the chamber, and then start drying time count while vacuum is still being made.
Throughout the drying process, the jacket is kept at working pressure with hot steam. In this way, the
high vacuum and heat radiation from the chamber walls helps drying the material. - Cooling:
Once sterilization is done, slow vacuumize made until pressure drops to 1.100 mbar. After that, while
the vacuum system is still working, vacuum break valve opens preventing drop of pressure and thus
accelerating the cooling process. The phase ends when cooling ending temperature is reached.
Specification:
Design pressure | 0.245Mpa | Vacunm | -0.095Mpa |
Working Pressure | 0.22Mpa | Steam Source Pressure | 0.4-0.6Mpa |
Design Temperature | 139ºC | Water Source Pressure | 0.1-0.3Mpa |
Working Temperature | 134ºC | Compressed Air Pressure | 0.5-0.7Mpa |
Specifications | Overall Dimensions | Chamber Size | Steam Consumption | Power | Water Consmption | Net Weight |
Model | L*M*H(mm) | L*W*H(mm) | (kg/cycle) | (KW) | (kg/cycle) | (kg) |
Single/Double Door | ||||||
YG-0.1 | 825*1080*1600 | 630*400*480 | 15 | 1 | 80 | 380 |
YG-0.25 | 895*1220*1720 | 760*600*600 | 20 | 1.5 | 150 | 650 |
YG-0.36 | 1195*1220*1720 | 1000*600*600 | 25 | 1.5 | 150 | 760 |
YG-0.6 | 1245*1300*1880 | 1050*680*850 | 30 | 2 | 200 | 1100 |
YG-0.8 | 1595*1300*1880 | 1400*680*850 | 35 | 3 | 250 | 1300 |
YG-1.2 | 1695*1370*1960 | 1500*750*1100 | 40 | 3 | 300 | 1900 |
YG-2.5 | 3195*1370*1960 | 3000*750*1100 | 75 | 4.5 | 450 | 2800 |
YG-5.0 | 3635*1800*2200 | 3400*1000*1500 | 150 | 7.5 | 600 | 4500 |
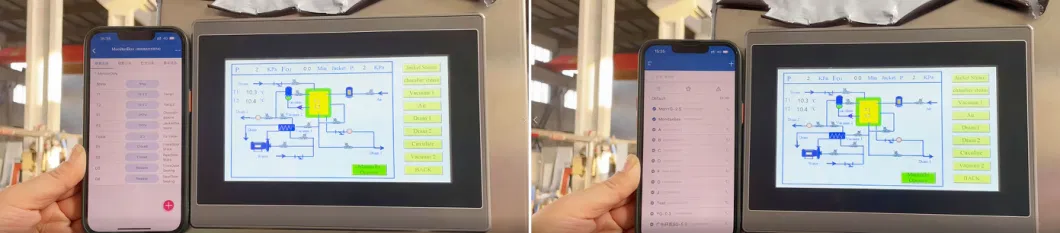
Details:
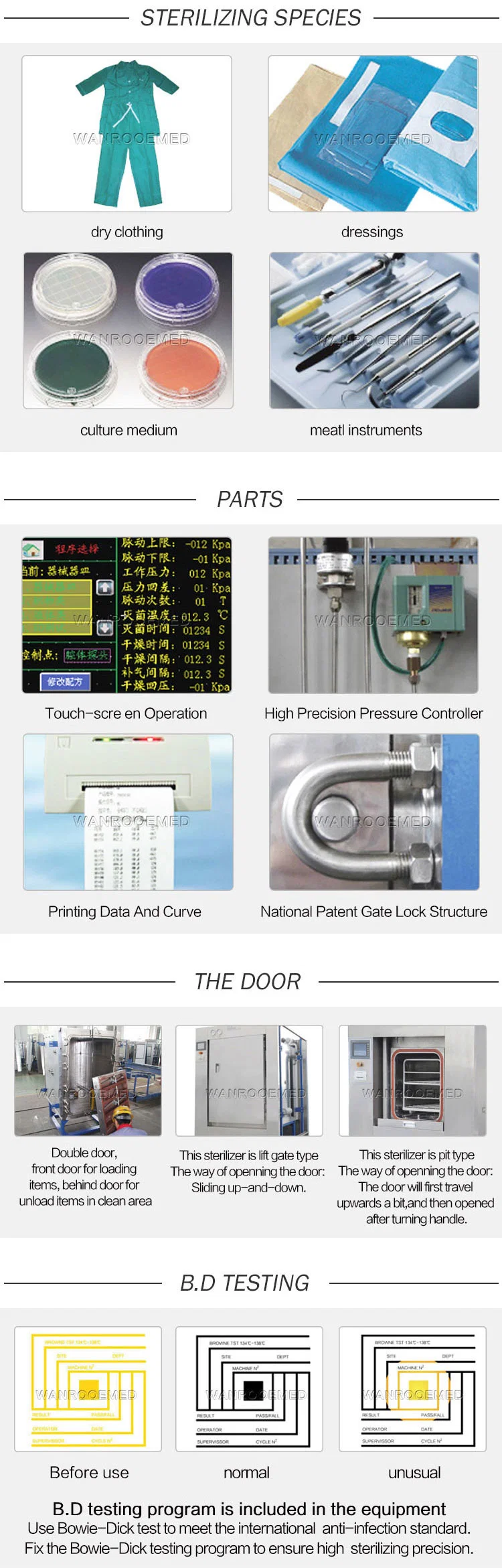
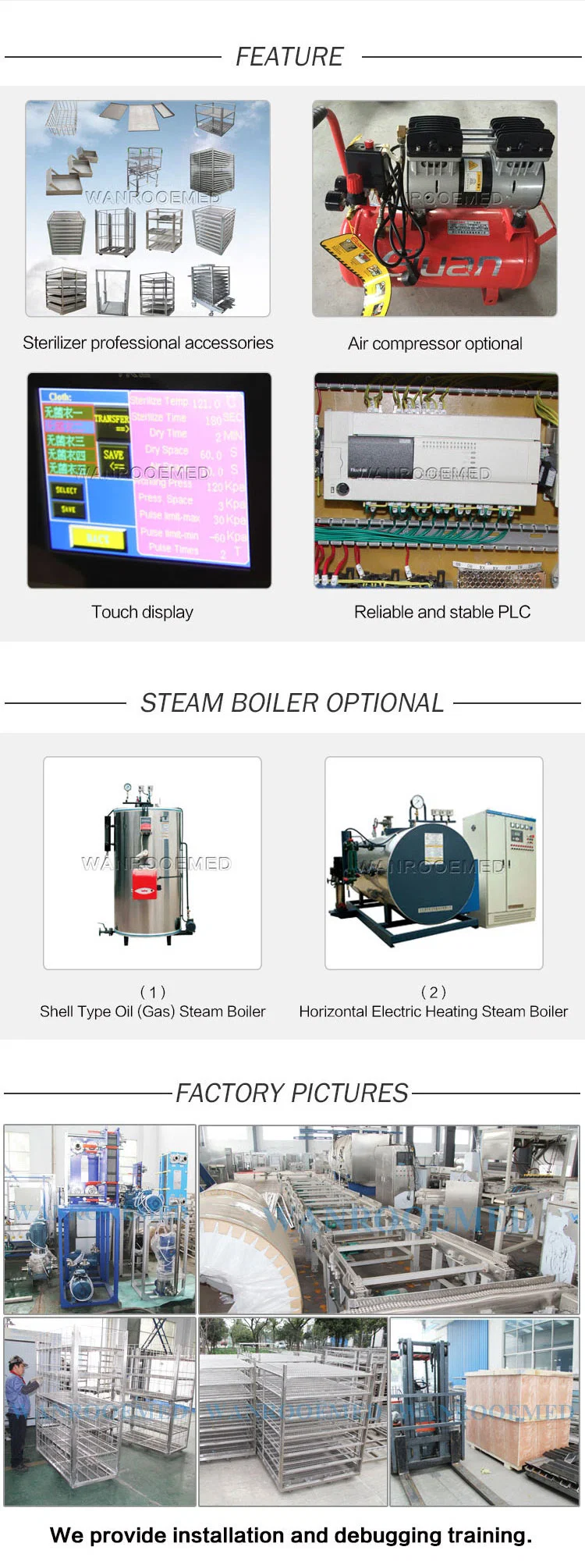
Company Information:
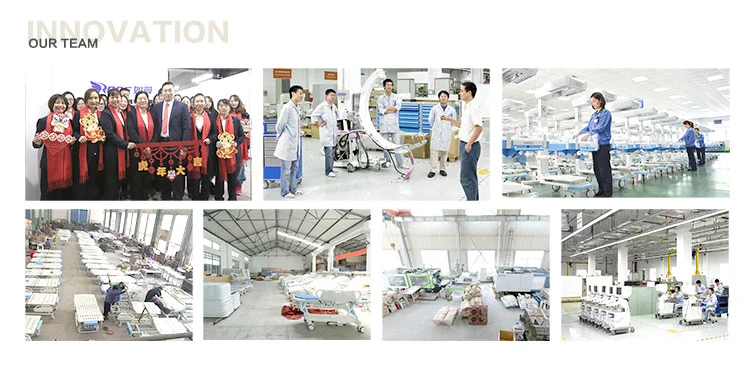
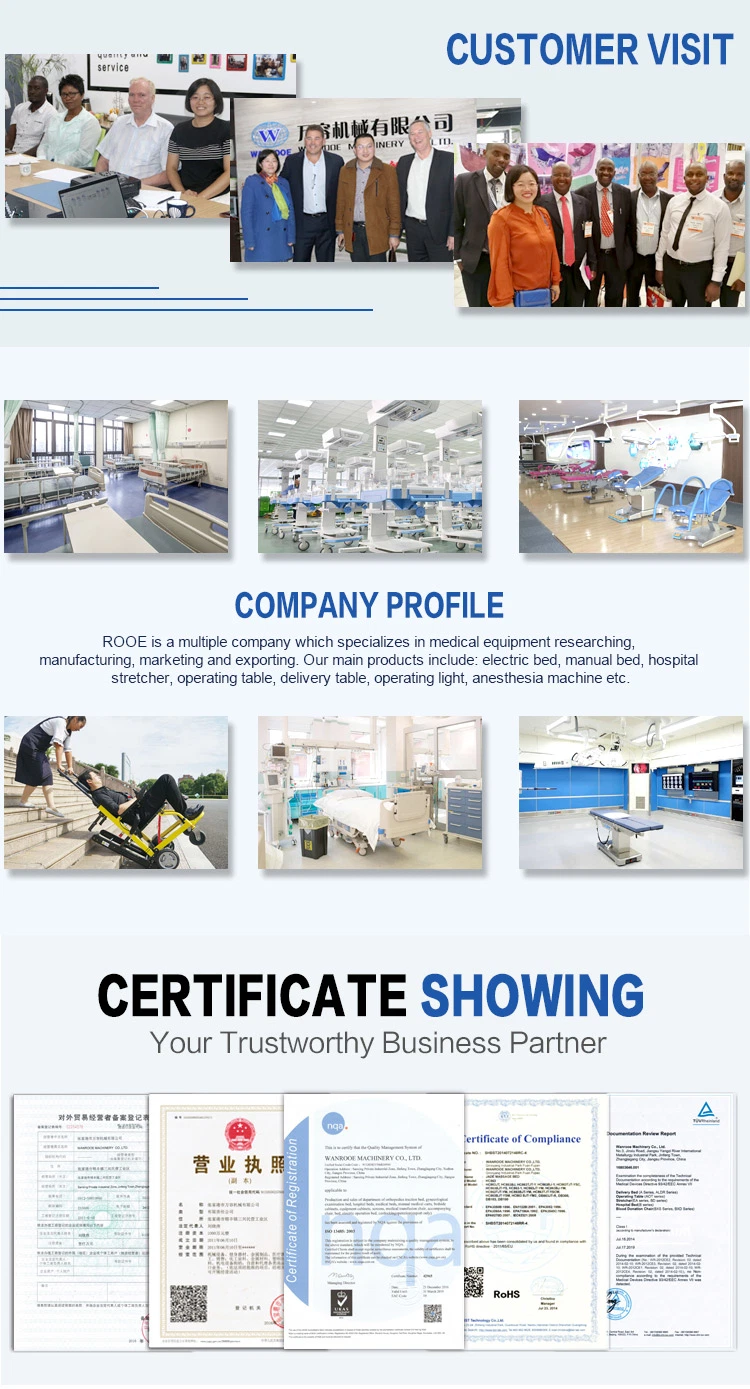